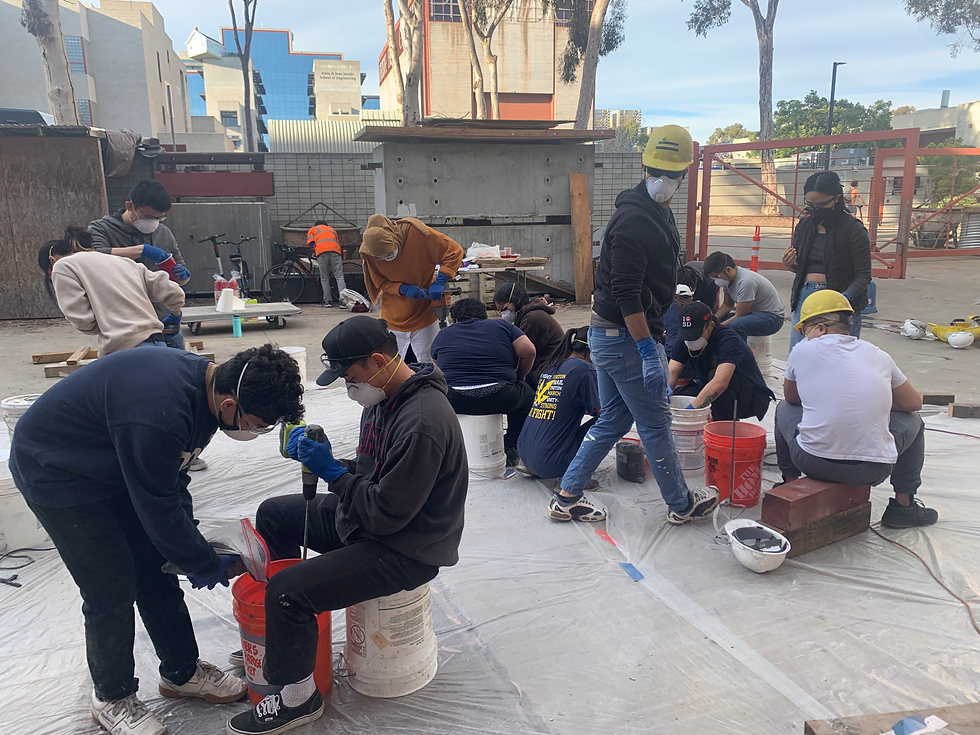
Meet our Subteams
UCSD Concrete Canoe team has 6 unique subteams that work collaboratively to effectively plan, design, and build our 20ft canoes on time for the annual ASCE Concrete Canoe Competition. Each team focuses on a different aspect of the canoe-building process, from structural analysis to visuals. Members are free to explore and participate in one or multiple teams. Check out what each of our subteams do!
Tech Team
The tech team is responsible for designing the hull of the canoe. They use software including MAXSURF Stability and Solidworks to conduct structural analysis and calculations in order to create an operable design with maximum performance in terms of stability, maneuverability, and speed. Members of tech team are required to have a strong understanding of engineering principles and CAD software to be able to conduct iterative design to find the best combination of design factors. The design also must take into account the carrying capacity of the paddlers and durability during transport, hence load-bearing analysis is also involved. The goal of the tech team is to generate a hull shape that maximize each design factor while allowing paddlers maximum access to water. Tech team works closely with the mix team as well as the construction team such that mix team will examine the overall design to determine the allowable slump of the concrete while construction team will use the hull design to construct the styrofoam mold for the canoe.
​

Mix Design Team
Our mix design team is responsible for creating all of the different concrete mixes that will be used to construct the canoe, including the structural mix and aesthetic mix. Mix design must consider and balance between factors of strength, workability, and density of concrete in order to produce a lightweight, high-strength concrete mix that is both buoyancy and capable of sustaining high-stress loads of the paddlers.
​
The team must research new cementitious materials, aggregates, and admixtures to determine which materials would best align with the annual rules and achieve optimal performance. Throughout the fall quarter, iterative mixing and testing are done multiple days a week as concrete takes about 14-28 days to properly cure- it is important that we create as many mixes as soon as possible in order to best determine our finalized mix. Mixed concrete is placed into testing cylinders and slab molds. Once cured, they are taken to the lab to undergo tensile and compression tests. We analyze and compare these numbers between all of our test mixes in order to conclude our final mix for the canoe.
​
​

Mix leads mixing fresh concrete
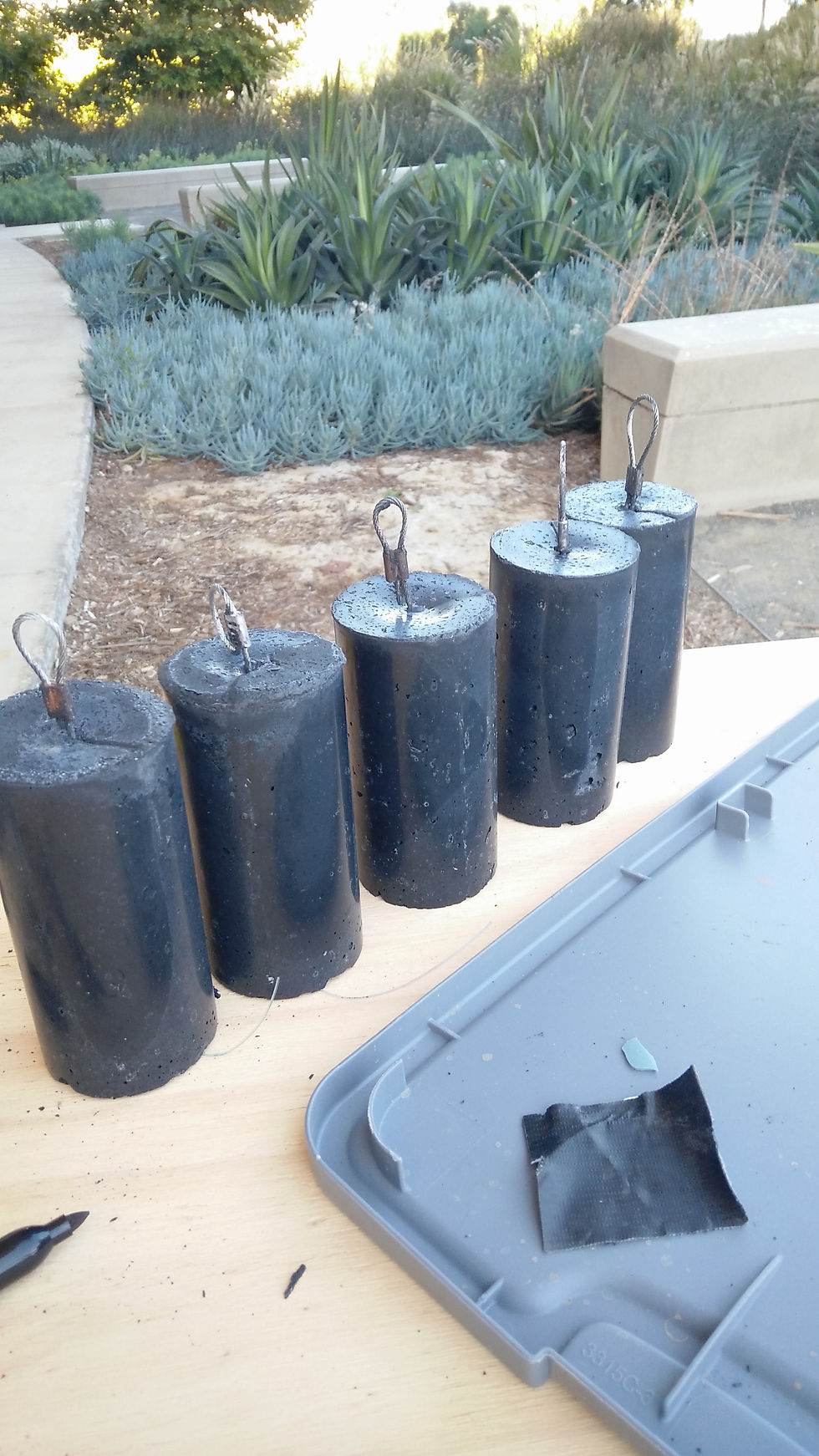
A collection of testing concrete cylinders

Tamping concrete to pack in the concrete and reduce air bubbles

Mix leads mixing fresh concrete
To give a brief Concrete 101, here are some helpful definitions and concepts we often refer to during mix meetings:
We use three types of ingredients in a test mix:
-
Cementitious Materials: Cementitious materials appear powdery and constitute the most volume out of the other ingredient types in the mix. They are responsible for contributing to the overall strength of the concrete mix and are highly reactive to water. Examples include slag, VCAS, Portland cement, silica fume, and hydrated lime.
-
Aggregates: Aggregates are considered as filler material in concrete and are added after mixing the cementitious materials. Aggregates come in various sizes and it is important to add them in order from the largest size to the smallest size (gradation) in order to fill in any potential gaps that may form within the mix. Holes in the mix will weaken the concrete since it is not completely packed in and aggregates help to reduce that. For Concrete Canoe, we choose aggregates with a low specific gravity in order to reduce the density of the concrete and ensure buoyancy. Specific gravity is the relative density according to a given reference material. Examples include Poraver, Utelite, and Q-CEL.
-
Admixtures: Admixtures are various chemical liquids (aside from water) added to the concrete mix. Each type of admixture affects the mix differently. For example, we commonly use Plastol to reduce the amount of water added and Eucon DS Air Entrainer to create tiny air bubbles to reduce density.
The water-cement ratio is a very important proportion in mix design since it greatly affects the strength and workability of the concrete. Too much water will increase slump (the fluidity of the concrete) and decrease workability as well as strength, whereas too little water will decrease slump but make the mix too brittle. An optimal ratio must be used in order to meet all desired conditions of the concrete.
​
![]() | ![]() | ![]() | ![]() |
---|

Using hot-wire cutters to fabricate mold
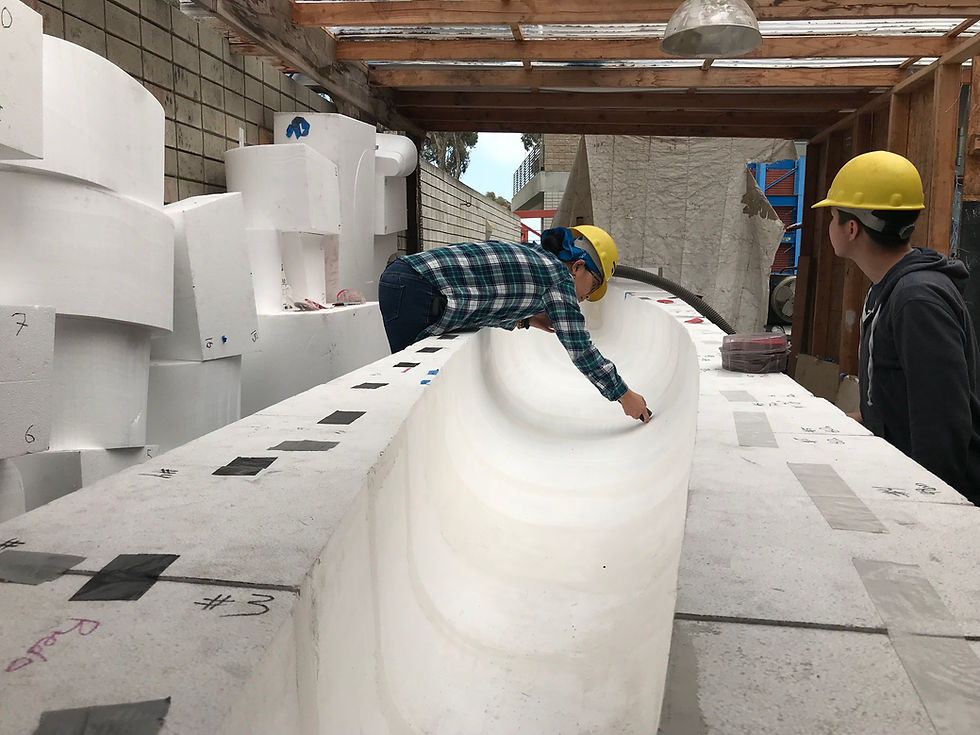
Styrofoam mold fabrication

Pre-tensioning system

Using hot-wire cutters to fabricate mold
Construction Team
The construction team is responsible for the fabrication of the styrofoam mold that the canoe is made in as well as setting up the tensioning system for the concrete to increase tensile strength. Additionally, they construct the transporter that transports the canoe to the competition. Members of construction team are expected to use power tools such as sanders, hot wire cutters, and grinders to execute these projects. They work closely with tech team in order to create the mold for the hull of the canoe. During Pour Day, they oversee the fabrication of the canoe and ensure safety and quality. During the summer, they are responsible for researching different techniques during the design stage to ensure proper preventive measures are donducted for safety.
​
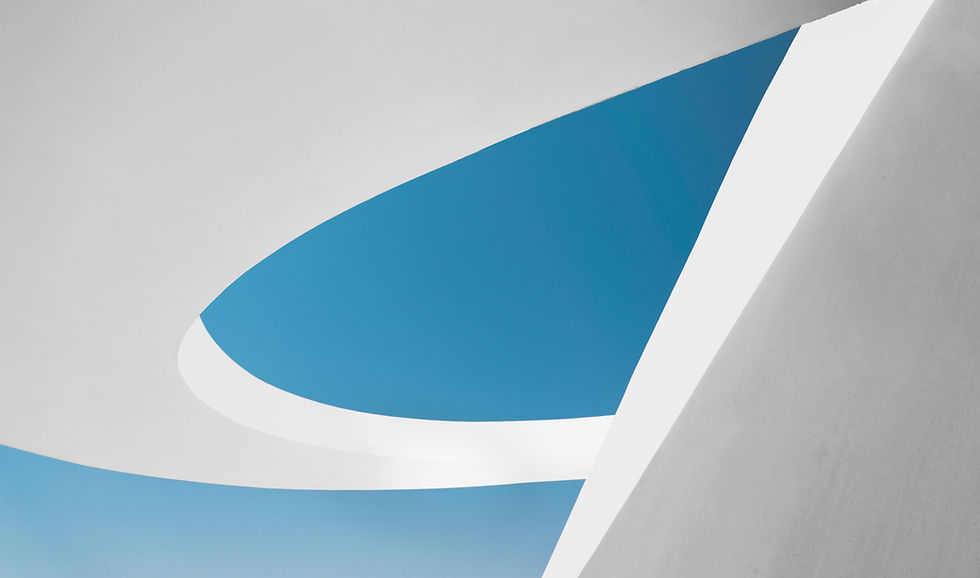
Aesthetics Team
Our aesthetics team focuses on the visuals of the canoe as well as the overarching theme present in our PSWS display table, apparel, technical report. They are also responsible for creating graphics to advertise our project team on our Instagram and Facebook page. They work closely with the mix design team to discuss approaches to create a practical, yet creative design that uses cement pigments and materials that meet ASTM standards. These designs are created using neoprene inlays, which are laser-cut designs in neoprene (synthetic rubber) sheets that are placed on the concrete to preserve shapes to be filled with other colored concrete.
​​
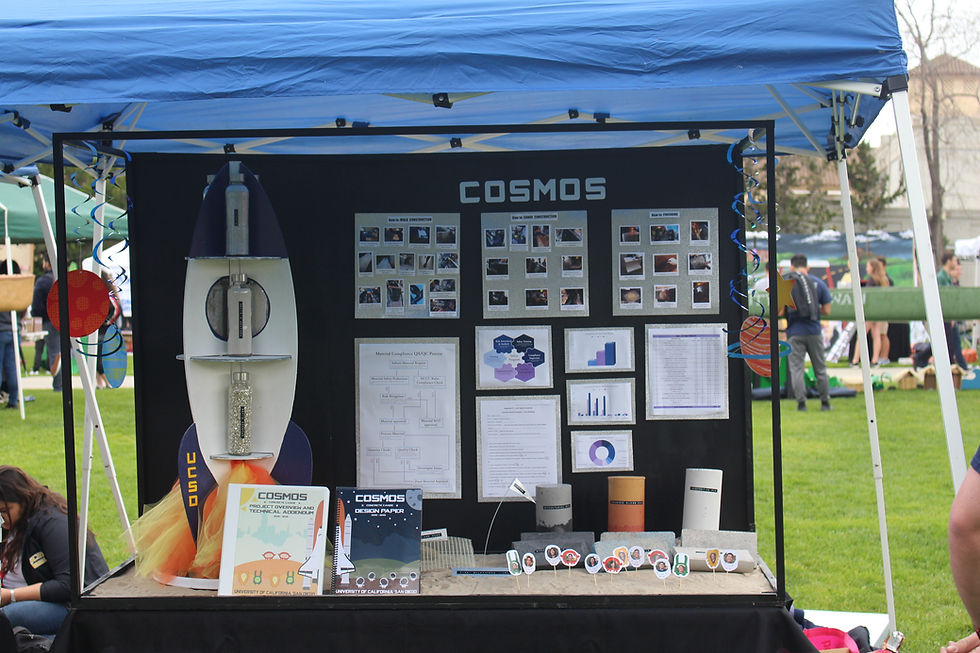
Display table for Cosmos (2019)

Shirt designs for PSWS

Aesthetic mix samples
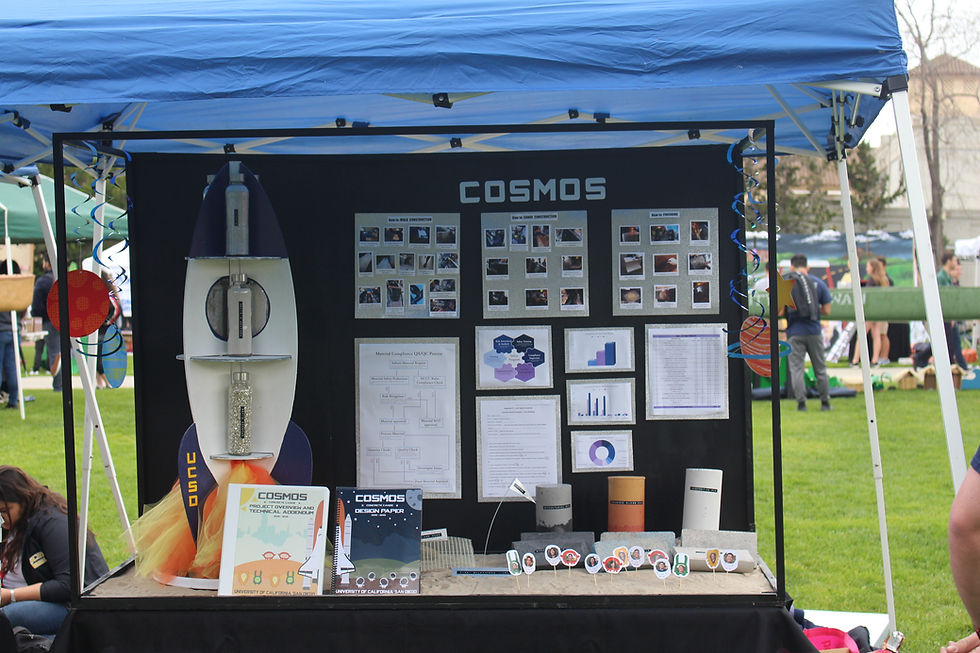
Display table for Cosmos (2019)

Finance Team
The finance team keeps track of the team's funds from social events to construction materials. Funds are raised through sponsorships, grant writing, and scholarships every year, yet our team works hard to seek additional sponsors and maintain existing partnerships with alumni and industry professionals. ​Their most important duty is completing the Matching Grant, a grant provided by the UCSD IDEA Center. The finance team works closely with the Vice President of Finance in SCSE to record income and expenditures and writes about budget and fundraising in their respective section of the technical report.
​
QA/QC Team
The QA/QC team (Quality Control) oversees and ensures a safe working environment, making sure that all members wear personal protection equipment (i.e. hard hats, N95 masks) whenever they are working in the shed. Adopting and enforcing safety regulations, they work to reduce the risk of accidents during the construction phase and during Pour Day. The team ensures that all materials used in the canoe's fabrication meet C4 criteria and guarantees quality by teaching members safe, sustainable construction and mixing processes. In midst of the COVID-19 pandemic, the QA/QC also ensures that COVID-19 policies are respectfully followed and that in-person meetings are safe. ​
​
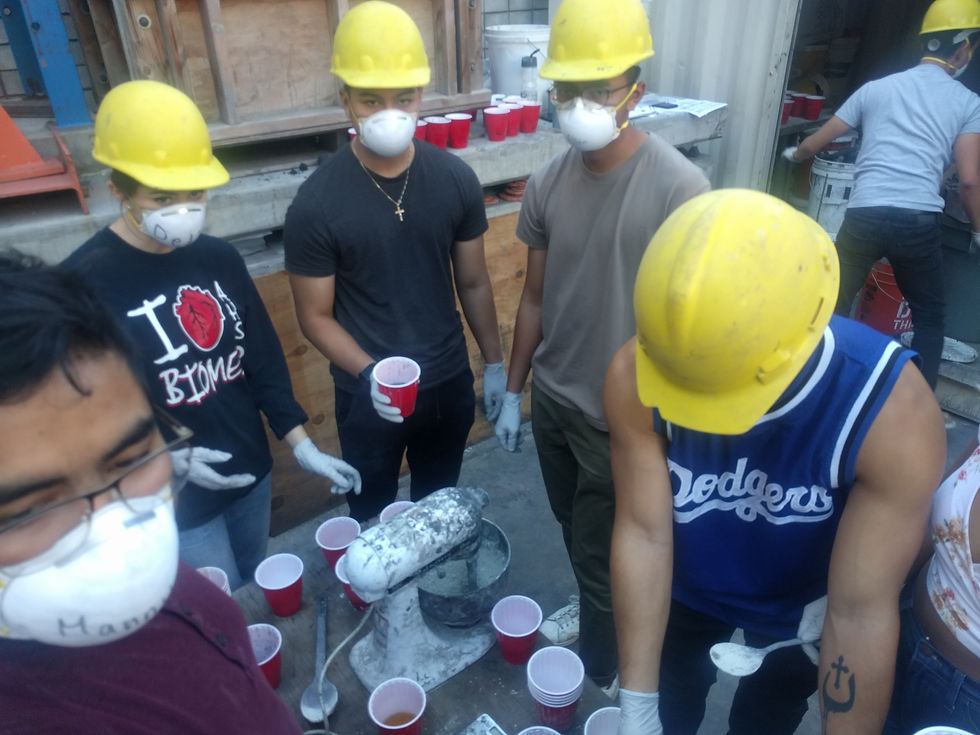

N95 masks and hard hats are very important for safety!

Using hot-wire cutters to fabricate mold
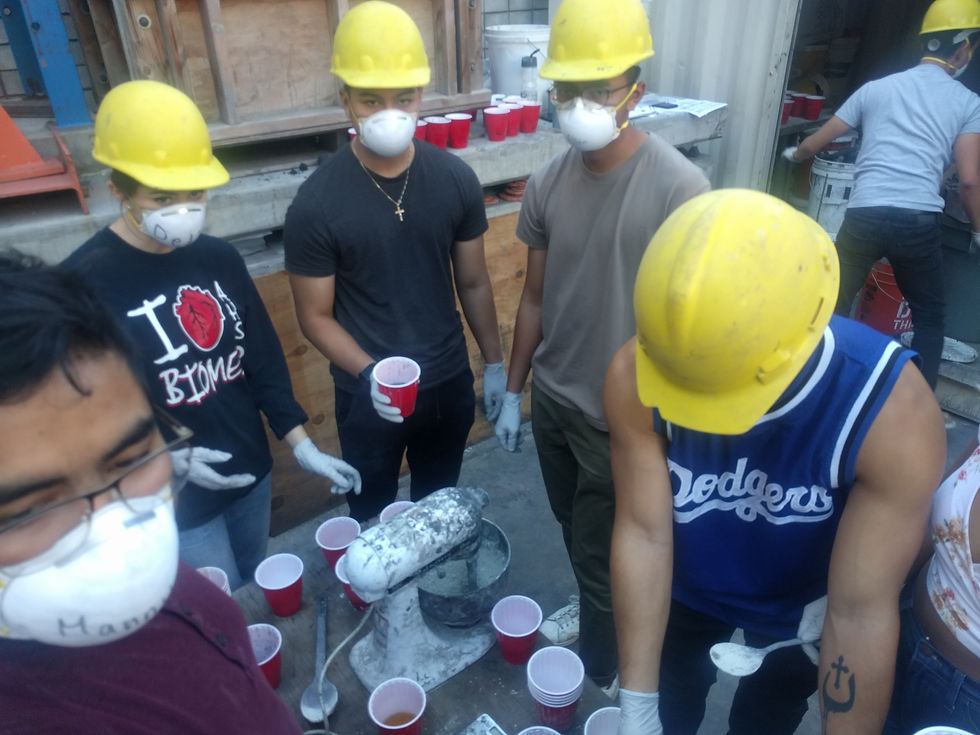